Kaveri & Aero-Engine: News & Discussion
-
- BRFite
- Posts: 287
- Joined: 11 Aug 2016 06:14
Re: Kaveri & aero-engine discussion
Shreeman sar ji
That was my rant all the time, even if the MTBF low fail too often and require maintenance of home grown engine, even if it gas guzzler it's better to make it and try it. The Chinese have WS clones of Russianengines that way...
I was saying if Kaveri was proven to be half as good in tests with Russian aircraft at altitudes
Then let's make 25Kn engine and fit it to one time use like UAV, or if it's reliable enough mate it with air frame that can take twin engines and...
I was judged to be a fool, that is nothing new, but I am still employed and make a decent salary, of course stand up is my other job
That was my rant all the time, even if the MTBF low fail too often and require maintenance of home grown engine, even if it gas guzzler it's better to make it and try it. The Chinese have WS clones of Russianengines that way...
I was saying if Kaveri was proven to be half as good in tests with Russian aircraft at altitudes
Then let's make 25Kn engine and fit it to one time use like UAV, or if it's reliable enough mate it with air frame that can take twin engines and...
I was judged to be a fool, that is nothing new, but I am still employed and make a decent salary, of course stand up is my other job
Re: Kaveri & aero-engine discussion
Well, GE has pioneered the laser based construction, which actually they claim provides better features, therefore requireing less air to cool - more air for the engine itself.vina wrote:Surely they cannot use 3D printing (or even casting) on single crystal blades. It is that last 200 to 300 deg difference in material capability that makes such a vast difference in overall engine performance. There is no real substitute for the traditional methods for turbine blades of higher performance engines.So with 3-D printing technology, now it is possible to provide casting patterns without the use of wax or ceramic injection dies. So now it’s possible to take a 3-D CAD, convert it into various cross-sectional layers directly build 3-D ceramic shells, with all inbuilt intricate-cooling paths etc, into which metal can be poured
Not that I have a quibble with what they are doing for this 25KN engine, this rapid prototyping and testing and iterative development is the right strategy.
However, we need to wait to see what exactly is being provided to India via the DTTI. For sure India wanted certain techs and seem to have been granted permission from the US DoD (but not yet from SD?). For sure it is not a secular tech.
-
- BRF Oldie
- Posts: 3762
- Joined: 17 Jan 2007 15:31
- Location: bositiveneuj.blogspot.com
- Contact:
Re: Kaveri & aero-engine discussion
More and more, spinster sahib, I am reduced to see the river of life float by. Consigned to mere pH measurements from shore without getting toes wet. There sure is a lot of ammonia in the water. Yet people keep telling me its fit to drink, the swamp gas is harmless, and all is good with the world. I am not so sure, soil samples, wind vanes, and all the test tubes of yellow liquid tell me nothing is as it is described in the world even if it is not my bees wax.Spinster wrote:Shreeman sar ji
That was my rant all the time, even if the MTBF low fail too often and require maintenance of home grown engine, even if it gas guzzler it's better to make it and try it. The Chinese have WS clones of Russianengines that way...
I was saying if Kaveri was proven to be half as good in tests with Russian aircraft at altitudes
Then let's make 25Kn engine and fit it to one time use like UAV, or if it's reliable enough mate it with air frame that can take twin engines and...
I was judged to be a fool, that is nothing new, but I am still employed and make a decent salary, of course stand up is my other job
There is always reason for things to be as they are. Just not the one one hears. And usually just the bigger entity upstream. We are merely recycling.
Re: Kaveri & aero-engine discussion
Engine of indigenisation
The defence ministry estimates that India will buy foreign military aero engines worth Rs 350,000 crore {$5.3 billion over 20 years or 0.265 billion per year}over the next two decades. While indigenising our military fleet, successive governments have neglected the development and manufacture of aero engines, which account for one-third the cost of a new military aircraft. Unless we build a significant percentage of our own engines, Defence Minister Manohar Parrikar cannot succeed in his stated ambition to increase defence indigenisation from the current 40 per cent to 70 per cent within a decade.
Take the expense on engines for India’s on-going helicopter programmes. Hindustan Aeronautics Ltd (HAL) will build at least 400 Dhruv helicopters and about 180 light combat helicopters (LCH), both twin-engine choppers. Another 400 light utility helicopters (LUH), with single engines, will replace the current fleet of Chetaks and Cheetahs. Each LUH will consume 3 – 3½ engines over its service life, while the twin-engine choppers will each require 6 – 7 engines, adding up to some 5,000 Shakti engines over their service lives. At the Shakti’s current price of eight crore rupees, this adds up to Rs 40,000 crore. Add inflation and the cost of replacing components that fail, and the consumption of gaskets and bearings, and the figure would exceed Rs 50,000 crore.
India’s defence industry has done well to master aeronautical design, flight dynamics, control laws, avionics and other skills needed for building modern aircraft. Yet, for a variety of reasons, mostly relating to poor technical-strategic vision and planning, every aero engine flying in India is, and will continue to be, purchased from abroad.
The world’s big engine vendors --- America’s General Electric, Honeywell and Pratt & Whitney; Europe’s Rolls-Royce and Snecma; and Russia’s Klimov and NPO Saturn --- are happy to sell India aero engines. There are seldom technology-protection aspects to engine sales, because reverse-engineering them is very difficult. Key aero engine technologies relate to materials (high-temperature composites and alloys); and precision engineering, which are difficult to copy. Tellingly China, that master of reverse engineering, has not succeeded in developing a high-performance aero engine. The Guizhou Aircraft Industry Corporation has spent two decades working on the Taishan turbofan engine for the JF-17 Thunder fighter that Pakistan has inducted into its air force with a Russian Klimov RD-93 engine. Even after spending a reported $10 billion, the Taishan’s performance has satisfied neither the Chinese, nor the Pakistanis. Now Beijing is scaling up the effort, investing a reported $40 billion and training thousands of engine designers.
Yet, India has never prioritised aero engine development, and put vision, money and manpower into this. There was irony last week, when Mr Parrikar visited Bengaluru to inaugurate a new 25 kiloNewton (kN) engine built by Hindustan Aeronautics Ltd (HAL) for its trainer aircraft. Overlooked was the fact that, three decades ago, HAL had developed a 25kN engine for upgrading its successful Kiran trainer into the Kiran Mark II. When that engine was nearing completion, the defence ministry decided to ground the (also indigenous) HF-24 Marut fighter. This made available the (slightly used) engines of 174 Marut fighters --- the Orpheus 703 engine, built by Bristol-Siddeley. Those 30 kN engines were de-rated to 25 kN and put into the Kiran Mark II. HAL’s indigenous engine went to the scrap heap.
Over succeeding decades, the engine development fiasco continued similarly, with the Defence R&D Organisation (DRDO) making only limited headway in developing the Kaveri engine for the Tejas light combat aircraft (LCA). While the Tejas needs an engine with 82-90 kiloNewtons (kN) of peak thrust, the Kaveri has only managed 72 kN during flight testing in Russia. This is inadequate for a modern fighter, but the DRDO is still seeking a technological breakthrough with very limited resources. The total budget for the Kaveri, including on engineering and test facilities, has been limited to Rs 2,839 crore (defence minister to parliament in December 2012).
True, India cannot throw money at the problem the way Beijing can. But it does not need to, since it has a model to replicate --- India’s successful missile development problem. This involved clearly identifying an aim, allocating technological manpower and leadership, and spending about enough to keep the projects going. Even with a frugal approach, which is all we can afford anyway, a high-performance jet fighter engine project would require at least Rs 14,000-15,000 crore{$2.26 billion, that is it?}.
The defence ministry already has a working proposal for this. Prepared by the DRDO, it includes a detailed breakdown of the technological requirements; identifies the specific materials and technologies that must developed or obtained from abroad through partnerships; identifies the production technologies needed and essential test facilities.
Currently, when the DRDO needs to test the Kaveri, it is flown to Russia, along with a flight test team, to the Gromov Flight Research Institute outside Moscow. Here, it is fitted onto a Russian IL-76 aircraft and its performance evaluated in flight. Before flight tests, it must undergo ground checks at Moscow’s Central Institute of Aviation Motors, in simulated altitudes up to 15 kilometers (49,200 feet). Creating such flight-testing facilities in India would save hundreds of crores and a great deal of time.
Sadly, the defence ministry is not fast-tracking the proposal. It has been discussed internally, and with private sector representatives. It was decided that roles and responsibilities should be allocated to individual organisations and firms. And there the matter stands.
Mr Parrikar must move with alacrity to institute a strong management structure, like the “LCA Empowered Committee” that overseas the Tejas project. Chaired by the defence minister, this team would monitor and coordinate. Under this apex council should be an executive body, headed by DRDO’s aerospace director, with representation from all stakeholders, including private industry. This should oversee development, creation of test facilities and training of technological manpower.
The time is propitious. Earlier this month, during Mr Parrikar’s visit to the US, Washington conveyed its willingness to “expand cooperation in production and design of jet engine components.” This will open the doors to joint development between US engine-makers, particularly General Electric, and Indian entities like the DRDO. Tapping into America’s vast experience in this field would help the DRDO overcome some of the hurdles that have bedevilled the Kaveri programme.
Re: Kaveri & aero-engine discussion
UPA ki qtiyapa all coming out, so much so they were running around asking for half a million $. While BR was busy cursing GTRE, check out the reality. And now hopefully the new GOI gets some brains and supports the program.
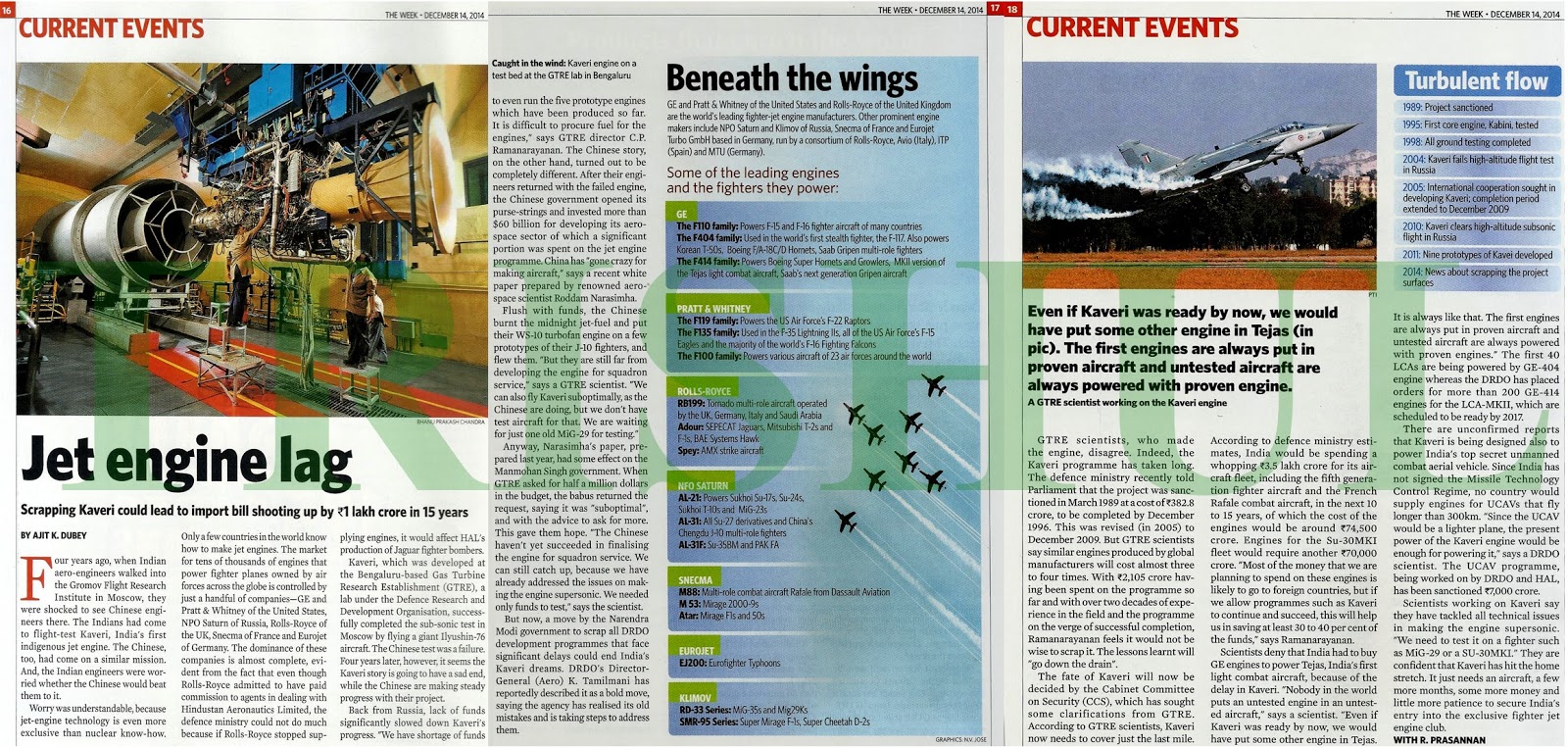
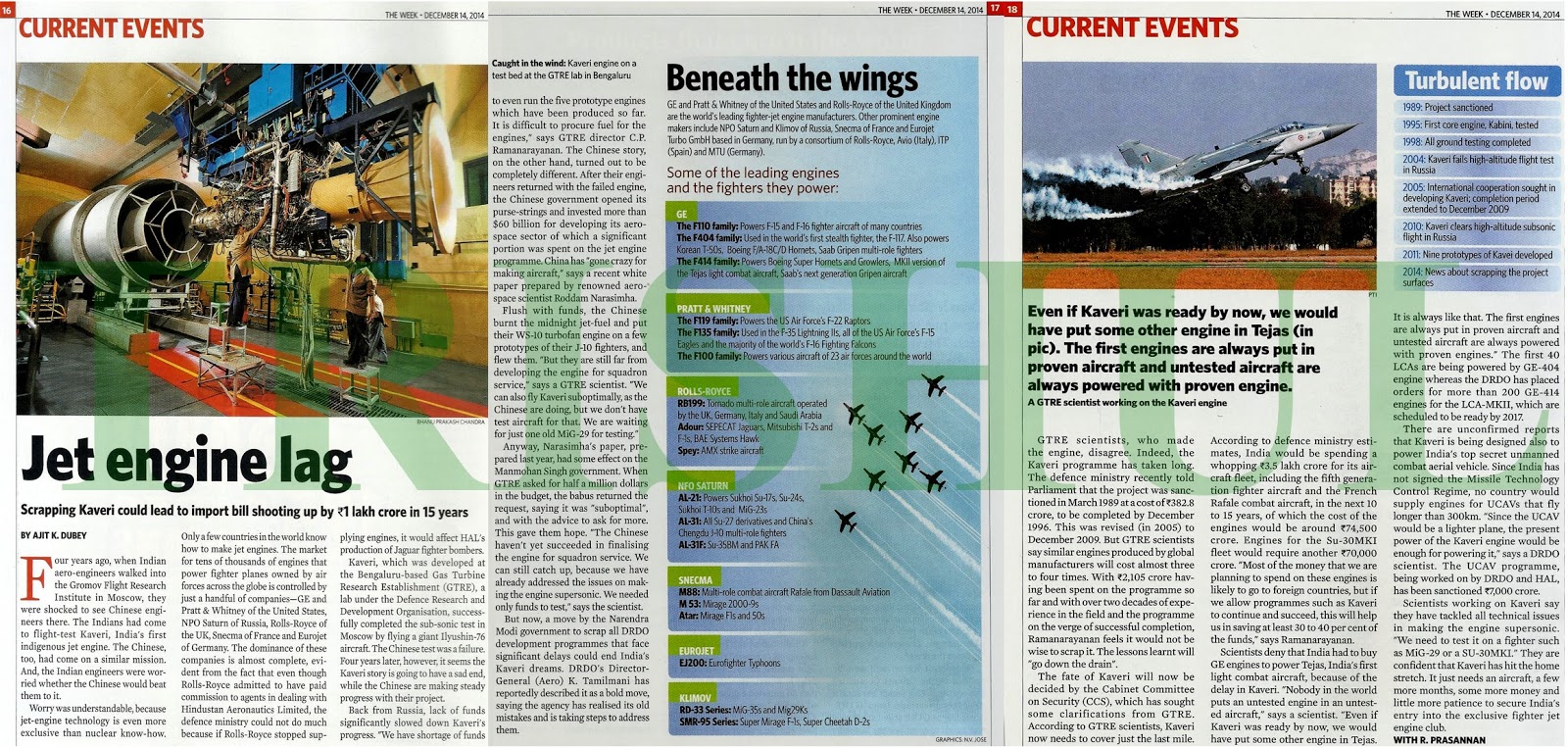
Re: Kaveri & aero-engine discussion
^^^
Let's hope India will take Kaveri to its completion and not abandon it after reaching this far! India needs to spend money on enabling infrastructure, such as wind tunnel facilities, test aircrafts, etc. Given peanut budget, Indian scientists/engineers have achieved a lot. Imagine if they were/are properly funded...
Let's hope India will take Kaveri to its completion and not abandon it after reaching this far! India needs to spend money on enabling infrastructure, such as wind tunnel facilities, test aircrafts, etc. Given peanut budget, Indian scientists/engineers have achieved a lot. Imagine if they were/are properly funded...
Re: Kaveri & aero-engine discussion
There was the GATET initiative to develop the core technologies we lack and a family of GT aero engines. There has been no news under that banner since inception. Is that still alive?
-
- BRFite -Trainee
- Posts: 31
- Joined: 11 Aug 2016 06:14
Re: Kaveri & aero-engine discussion
Let's go on the streets in support of completing the kaveri development. We could ask kejriwal and hazare for their support,they will surely support in the name of swadeshi product. 

-
- BRF Oldie
- Posts: 4111
- Joined: 30 Jul 2004 15:05
- Location: Spectator in the dossier diplomacy tennis match
Re: Kaveri & aero-engine discussion
http://aviationweek.com/awinbizav/india ... ine-design
India Launches New Helo Engine Design
(Admins: New thread for all Aero engines needed )
India Launches New Helo Engine Design
(Admins: New thread for all Aero engines needed )
Re: Kaveri & aero-engine discussion
Certified Gipsy @CertifiedGipsy 1h1 hour ago
@SJha1618 Saurav, what is the latest status of GTRE Kaveri Engine? Do we have a working Engine? What are its latest features?
Saurav Jha @SJha1618 38m38 minutes ago New Delhi, Delhi
@CertifiedGipsy Tested to 72 + KN. Flew for more than 50 hours on the FTB in Russia. Program continues. Rechristening soon.
Certified Gipsy @CertifiedGipsy 30m30 minutes ago
@SJha1618 Doesn't it mean they have a working engine at 80kN?
Saurav Jha @SJha1618 28m28 minutes ago New Delhi, Delhi
@CertifiedGipsy What it means is that they have a prototype engine that has achieved 90 % of its designed wet thrust capability.
Certified Gipsy @CertifiedGipsy 25m25 minutes ago
@SJha1618 Brilliant. Also, is it possible for them to to fit two of these Engines in existing MiG 29 and see how it performs?
Saurav Jha @SJha1618 24m24 minutes ago New Delhi, Delhi
@CertifiedGipsy Only one engine will be fit first. Standard practice. 20 unit run is to get to a stage where you can talk about MTBO etc.
Saurav Jha @SJha1618 25m25 minutes ago New Delhi, Delhi
@CertifiedGipsy 90% of the required thrust with existing materials. The 20 new ones will see product improvements leading closer to 80 KN.
Certified Gipsy @CertifiedGipsy 23m23 minutes ago
@SJha1618 But wiki says that the full after burner thrust is 81kN and planned to be upgraded to >95kN. Don't know what their source is.
Saurav Jha @SJha1618 20m20 minutes ago New Delhi, Delhi
@CertifiedGipsy 90 KN is the final design goal. 95 KN will reduce engine life. 81 KN not achieved yet for legacy prototypes.
Certified Gipsy @CertifiedGipsy 19m19 minutes ago
@SJha1618 90kN would be a great achievement. We can power both single engine jets and twin engine variants with indigenous engines.
Saurav Jha @SJha1618 17m17 minutes ago New Delhi, Delhi
@CertifiedGipsy That is the idea.
Re: Kaveri & aero-engine discussion
Thanks hanumadu for that update from SJha
Re: Kaveri & aero-engine discussion
Re Maitya
I suppose 25kn engine can also lead to offshoots in the form of 2500-3500hp turboshaft and turboprop engines for our IMRH helo and RTA aircraft?
I suppose 25kn engine can also lead to offshoots in the form of 2500-3500hp turboshaft and turboprop engines for our IMRH helo and RTA aircraft?
Re: Kaveri & aero-engine discussion
Of course ... see from a layman pov, a turboshaft is basically a turbojet (and not a turbofan) with a shaft sticking out of the turbine backwards (along-with a gear reduction system) which drives the main rotor - this rearward shaft assembly replaces the exhaust nozzle of a turbojet, and instead the post-LPT gas exhausts are expelled thru a split (laterally inverted U) exhaust system.Gyan wrote:Re Maitya
I suppose 25kn engine can also lead to offshoots in the form of 2500-3500hp turboshaft and turboprop engines for our IMRH helo and RTA aircraft?
So, if you have mastered the turbojet core (comprising of LPC-HPC-HPT-LPT) and have the sufficient knowhow of designing an appropriate reduction-gear system (free turbine ityadi concepts) you are more or less there.
Thus the key-word is the same-old same-old "turbojet core" know-how ...
Betw an APU is also a miniaturized turboshaft - and Kaveri/Kabini APU indigenous design/development was an unqualified success.
But then we all know about indigenous Main Gear Box (MGB) story* (refer below) of the ALH anyway, right?
Of course, this above is a mamoth over-simplification, but hope you get the drift!!
=================================================================
*ALH Dhruv: The Truth, First Hand – Hari Nair - from Livefist
<snip>
10. Main Gear Box(MGB).
(a) The MGB is designed to be compact, light-weight, yet capable of handling the high power output of the two turboshaft engines. It comprises only a two-stage reduction, with a large diameter central collective gear that has a titanium stub-shaft directly bolted onto it. The large diameter was mostly dictated by the need to run the control rods inside the rotor shaft. The stub-shaft in turn is attached to the titanium centre-piece that has the main rotor blades attached to it. The compact, squat and light-weight MGB frees up huge amounts of cabin space below, which is essentially the secret to the ALH’s excellent cabin volume. The project to develop the MGB was sub-contracted by MBB to ZF (Zahnradfabrik Friedrichshafen), Germany, a drive-train specialist that had previous aviation experience limited to developing and building gear boxes for the smaller MBB’s BK-117 and Bo-105 helicopters.
(b) Although ZF’s BK-117 MGB also uses a two-stage reduction, it has important differences in layout and geometry of the bevel and collective gears. Also, it handles only about half of the power of the ALH MGB. The first series of ALH MGBs were spectacular failures – these would not even last one hour of ground run on the Ground Test Vehicle (GTV). After every ground run, shed gear material would be found on the magnetic plugs indicating commencement of gear teeth failures. Initially ZF’s MGBs stubbornly refused to improve despite various efforts and this threatened to bring the whole project literally and figuratively to a grinding halt. After MBB (and ZF) left, it took our dedicated in-house transmission team many years of sweat and hard work, to recover the situation by going back to the drawing board, experiment with several remedial measures and introduce numerous modifications, so as to gradually bring the MGB to production standard. Obviously, this caused severe delays in the project.
<snip>
Last edited by maitya on 14 Jan 2016 13:52, edited 1 time in total.
Re: Kaveri & aero-engine discussion
You are welcome. Some of the information was already known here. In another tweet, he mentioned that Kaveri achieved the design dry thrust.Kailash wrote:Thanks hanumadu for that update from SJha
Re: Kaveri & aero-engine discussion
<deleted - duplicate post>
Last edited by maitya on 14 Jan 2016 14:42, edited 1 time in total.
Re: Kaveri & aero-engine discussion
Yes ... achieving dry thrust metric/value is quite an old news.hanumadu wrote:You are welcome. Some of the information was already known here. In another tweet, he mentioned that Kaveri achieved the design dry thrust.Kailash wrote:Thanks hanumadu for that update from SJha
However what is left unsaid is, and the more important aspect, is the failure to achieve the design dry TWR ratings - as the engine itself is overweight by 120-135Kg.
And it'll be a quite a challenge to shed those kilos without tinkering the core - for e.g. CFC based Fan, Ti MMC based compressor blades* (and discs) etc etc etc.
========================== *A bit of perspective of Ti MMC ===========================
1) Ti MMC (Metal Matrix Composites) provided 15-20% weight savings (compared to pure Titanium) - so first couple of stages of HPC compressor switching to Ti MMC would provide a modest weight savings.
2) But it's real gain is when compared with the nickel super-alloys, viz:
a) Density of 4.18g/cm3 vs 4.6g/cm3 vs 8.3g/cm3 (Ti-MMC vs Ti vs Ni-Superalloy)
b) Operating temp of about 760deg C vs 550-600deg C vs 1000-1200deg C (Ti-MMC vs Ti vs Ni-Superalloy)
The last two stages of the HPC of Kabini are based out of equiaxed-casted Ni-superalloys (as is the norm in most Turbofan cores of 90s - essential to withstand the 600+ deg C temp gradient across those stages - refer to the Kaveri sticky thread, for further details as to why is it so).
So if these last two superalloy based HPC stages switching to Ti MMC would provide a considerable weight savings (note the density diff mentioned above) - the industry benchmark is that Ti MMCs offer a potential of 50% weight reduction over nickel based superalloy based hotter compressor sections.
3) But another advantage is the specific stiffness of Ti MMC (242 GPa vs 200Gpa for Ti vs 207GPa of superalloys) if you are looking at using for it for the reinforced hollow fan blades - applicable when you are looking to have intricate cooling passages inside your compressor blades.
This (compressor blades with internal cooling passages) is actually quite typical of almost all cutting edge compressor stages of modern turbofans.
-
- BRFite -Trainee
- Posts: 31
- Joined: 11 Aug 2016 06:14
Re: Kaveri & aero-engine discussion
Does it really matter that engine is over weight by 150-200 kgs .. or it is 10 % below the expected thrust levels?? I don't think so. It is kind of 1st design of this class of engine and it works. How can we expect it to be as designed. More important is? 1. Is the engine reliable? 2. Can we put it in some existing aircraft and test it, certify it for limited series production? 3. get more data on those LSPs. We will need more iterations for that but we also need lots of data which can only be generated if we have multiple copies running in various vehicles.
Re: Kaveri & aero-engine discussion
What you are saying can be accepted if the engine were to be just an effort to build an engine.khedar wrote:Does it really matter that engine is over weight by 150-200 kgs .. or it is 10 % below the expected thrust levels?? I don't think so. It is kind of 1st design of this class of engine and it works. How can we expect it to be as designed. More important is? 1. Is the engine reliable? 2. Can we put it in some existing aircraft and test it, certify it for limited series production? 3. get more data on those LSPs. We will need more iterations for that but we also need lots of data which can only be generated if we have multiple copies running in various vehicles.
However, when an engine is "designed", then it needs to achieve the goals for which it was designed. Anything less is unacceptable. So, in the case of this Kaveri, it needs to meet both trust and weight (among others) goals. Else it cannot be part of another goal (the LCA?) and will be a tech demo, which is what you are asking for.
I had stated this about the Kaveri and the LCA - make them both some form of tech demos - and not the final products. Both need to succeed without the natural pressure/criticism.
-
- BRFite -Trainee
- Posts: 31
- Joined: 11 Aug 2016 06:14
Re: Kaveri & aero-engine discussion
Well I agree that if something is designed it should meet the criteria/spec which is the sole purpose of any design. Now leaving that slightly behind, I believe that you would agree it is extremely important to generate data on your first design and make it pukka before moving to next phase.there are no shortcuts in these kind of projects. Putting it into real use generates data related to maintenance, overhaul and life of the engines. This will enable you to learn these crucial aspects of your 1st design. And when you design your next iteration which is supposed to eliminate the 10% deficiency of 1 St design. Unless of course that the deficiencies are mission critical.
Re: Kaveri & aero-engine discussion
It makes it a tech demo. Which BTW is a GREAT idea, no two ways about it. In fact, India should have done that in the 50s, but a diff bed time story I guess.Now leaving that slightly (?) behind
I just do not see anything wrong in saying 'we did not achieve what we wanted to, but are going to reboot an d get it done right'. Use the old Kaveri to gather data, conduct research, etc and embark on a brand new, unrelated effort to get it right based on research. Start funding 100 universities with smallish amounts, in very specific fields. It will take money and time, but in 20 years India will not have to go looking for international partners and ToT and off-sets. Let the next gen be free? What a lot of people fail to visualize is that the decisions made today are impacting their kids/grand kids. THAT is a bigger failure than not having a Kaveri today, which has failed anyways (no shame).
Re: Kaveri & aero-engine discussion
Old Kaveri must fly on a Mig29 test bed as one of the engines! Need to get as much data as possible out of it.
-
- BRFite -Trainee
- Posts: 31
- Joined: 11 Aug 2016 06:14
Re: Kaveri & aero-engine discussion
NRao, Agree that accepting the failure to achieve what we wanted to is not wrong but it also is a very difficult thing to do. Morever my point is to power 20-30 planes with the K9 version so that lot of data can be generated today and not tomorrow (when K10 will come we don't know) in the real conditions. What would be wrong in powering Tejas Mk1 or and a squadron of Mig-29s with K9 unless we think it to be utter failure. K9 dry and wet thrust is equivalent to RD-33 and 404-IN. If there are other issues other than Weight and Thrust then please correct me.
But as you said its all a moot point to talk about K9 (the TD). All the user trials will be done with K10 only i guess.
But as you said its all a moot point to talk about K9 (the TD). All the user trials will be done with K10 only i guess.
Re: Kaveri & aero-engine discussion
So, yeah, use the Kaveri as a test-bed, essentially. OK.
But it needs to be clear that even that data will not really help a next generation of engines, which will require much better materials, processes, economics, etc.
So, I would go with a three streams: #1 the effort with GE, #2 a full spectrum pure research effort to fund umpteen universities and perhaps even some private institutions and #3 build on the Kaveri.
I would fund each of them independently, allow each of them to share info (if permitted) (but not share research - keep influence out), but *not* rely/depend on each other.
Somewhere down the road I would add #4 make a proper product - one which is viable in every way. If Kaveri is used to "gather as much data", then avoid making that engine a product and vice versa. Or make two groups, one o collect data from Kaveri and the other busy making the Kaveri a good product and let the two teams share information that benefits the other.
Finally, I would not orphan any one of them, but would certainly lean towards #1 (real short term) and #2 (real long term).
But it needs to be clear that even that data will not really help a next generation of engines, which will require much better materials, processes, economics, etc.
So, I would go with a three streams: #1 the effort with GE, #2 a full spectrum pure research effort to fund umpteen universities and perhaps even some private institutions and #3 build on the Kaveri.
I would fund each of them independently, allow each of them to share info (if permitted) (but not share research - keep influence out), but *not* rely/depend on each other.
Somewhere down the road I would add #4 make a proper product - one which is viable in every way. If Kaveri is used to "gather as much data", then avoid making that engine a product and vice versa. Or make two groups, one o collect data from Kaveri and the other busy making the Kaveri a good product and let the two teams share information that benefits the other.
Finally, I would not orphan any one of them, but would certainly lean towards #1 (real short term) and #2 (real long term).
Re: Kaveri & aero-engine discussion
Japan Ready For Next Fighter Engine Core
Aviation Week & Space Technology
Laying the groundwork for a fighter their country may field around 2030, Japanese engineers are preparing to build a demonstrator engine core, following success in materials research for the low-bypass turbofan engine they are planning for the aircraft. On the airframe side of the technology-acquisition program, another team has made much progress researching supersonic use of weapon bays for the proposed F-3 fighter.
A complete demonstrator engine, including a fan and low-pressure turbine, will follow the building of the core, says the defense ministry’s Technical Research and Development Institute (TRDI). IHI Corp. is the main contractor for the engine work, one of a range of projects Japan is undertaking in support of the F-3.
Airframe developers, probably including key personnel from Mitsubishi Heavy Industries, appear to have settled on something close to a 2013 configuration for the F-3 that emphasized endurance and weapons load over flight performance. TRDI has not confirmed the general arrangement of the aircraft has been decided, but its latest graphical presentation of the program uses previously seen drawings that approximate the 2013 configuration.
That design, 25DMU, described a heavy fighter with a belly weapons bay for six ramjet missiles about the size of the MBDA Meteor. The wing was large and slender by fighter standards, offering high fuel volume and low drag due to lift but penalizing acceleration.
TRDI presented an analysis in 2014 to show why that configuration was best. The key factor was that the high-endurance design provided more aircraft on station than would be available from an alternative fleet of high-performance fighters. By defending the configuration, which was compared with earlier studies, the agency gave outsiders reason to think an undisclosed design then in preparation, 26DMU, would not be much different.
The drawings republished in the latest report differ from 25DMU in two respects, probably because they slightly predate that design: They appear to show space for only four missiles in the bay, and an infrared sensor below and forward of the cockpit is absent.
While TRDI says in its presentation that building and testing the core will be the next step in engine development, with the complete turbofan to follow, it gives no timing for those activities. According to earlier planning, prototypes of the low-pressure compressor and low-pressure turbine will be tested from fiscal 2017 (testing started in fiscal 2015). A full prototype engine should be demonstrated in fiscal 2018, when the government is due to decide on whether to go ahead with the F-3. No doubt the government will want to see strong progress in engine development before committing to the fighter.
Testing of a compressor and combustor, the other two main modules of an engine core, has produced good results, says TRDI, without offering details on that work.
According to plans set at least three years ago, the demonstrator engine should generate 15 metric tons (33,000 lb.) of thrust and will be unusually slim, for reduced drag. Each F-3 would have two such engines. Like the Pratt & Whitney F119 of the Lockheed Martin F-22, the two-shaft Japanese engine is intended to have three fan stages, six high-pressure compressor stages and single-stage high- and low-pressure turbines that counterrotate. Barring upsets in testing, the main features of its configuration are likely to be settled. TRDI continues to present the engine with a drawing first shown in 2011.
In its progress update, TRDI confirms the average temperature of gas entering the high-pressure turbine will be as high as 1,800C (3,300F), a figure mentioned earlier in the program. Studies conducted so far indicate that ceramic matrix composite (CMC), a material that can cope with higher temperatures than metals, can be used to make the shroud of the turbine. The reinforcement of the ceramic will be carbon-silicon fiber. Stator and rotor blades will be made of a nickel-based single-crystal superalloy. The turbine disk, on which the rotor blades are mounted, will be built with a locally developed nickel-cobalt superalloy, TMW-24.
Five years ago, program managers expected to make the stator of CMC, while the rotor, a more challenging assembly, seems always to have been planned as metal. Japanese research suggests the rotor’s TMW-24 disk can be made through the traditional process of casting and forging, rather than by powder metallurgy, the usual technology for such rotor parts over the past few decades.
Researchers assessed TMW-24 on the basis of a disk life of 1,000 hr. under centrifugal stress of 630 megapascals (91,000 lbf. per sq. in.). Subject to those conditions a TMW-24 disk should cope with 710C, approaching the 730C performance of powder-metallurgy technology early in the previous decade, and above the 690C of the best cast-and-forged technology from the mid-1970s, TRDI reports. This aspect of the turbine has not yet been verified, however.
Weapons bay studies began in 2010 and were followed by tests beginning in 2013. That work has revealed combinations of supersonic airflow velocities and angles at which a weapon can be released from a bay. The next step will be the design of a release mechanism.
Japanese engineers are already familiar with dropping weapons from the bays of subsonic aircraft, such as the Kawasaki Heavy Industries P-1 maritime aircraft. The research into supersonic release from bays used computational dynamics and a wind-tunnel test rig that simulated the underside of an aircraft with an open weapon bay. The wind tunnel was capable of speeds of Mach 0.3-2.5. According to a 2012 report, release tests in the wind tunnel were conducted at Mach 1.4. That is a likely speed for the launch of an air-to-air missile. At the time of that report, 11 cavity shapes were being investigated.
Re: Kaveri & aero-engine discussion
We should produce Kaveri based AJT.
Re: Kaveri & aero-engine discussion
Yes ... and it has not got tested in the transonic and supersonic regimes*.Vivek K wrote:Old Kaveri must fly on a Mig29 test bed as one of the engines! Need to get as much data as possible out of it.
Plus all sorts of throttle setting, stall scenarios etc can only be encountered in a military platform - and not in transport-aircraft flying beds.
But for doing that the have first accumulate a certain amount of ground-test-run hrs (IIRC 3000hrs or thereabouts) before CEMILAC et all allows them anywhere near that to attempt it etc.
There was also some news reports wrt going for a Su-30 platform for this - after IAF refused to part with even a single 29 for this. Not sure where we are wrt these?
(*Note: Though a turbofan engine face, so the Fan face, wouldn't see transonic air-flow even though the platform itself may have been flying supersonic).
.
Re: Kaveri & aero-engine discussion
Why ask IAF for a platform, just get second hand MiG-29 from somewhere. Moldova, Yemen, USA, there was one on sale even in ebay a few years ago. Seems like russia has also restarted it's MiG-29 production since 2014. Here is hungary, eager to dispose off it's remaining MiG-29s for $43 million. Though this was back some 2-3 years ago, though wonderfully we had UPA raaj during this period, I believe there would still be airframes and running varients available.
http://bbj.hu/economy/tender-for-decomm ... gain_65772
24 MiG-29 for $43 million
https://www.strategypage.com/htmw/htpro ... 30528.aspx
http://bbj.hu/economy/tender-for-decomm ... gain_65772
24 MiG-29 for $43 million
https://www.strategypage.com/htmw/htpro ... 30528.aspx
Re: Kaveri & aero-engine discussion
There are enough scenarios where it can be produced in numbers. Ships, tanks, trains. Everyone showed interest, yet there are no big orders coming its way. Even assuming it cant fly reliably, or has low thrust to weight values, this has be mass manufactured for other roles and serviced. Just like research and test infrastructure, support, maintenance and spares manufacture is also an infrastructure(supply chain). We need atleast a handful of public/private companies capable of engine overhaul, refurbishment and upgrades to engines.
Re: Kaveri & aero-engine discussion
Just order an extra K version along with the IN order no?
Re: Kaveri & aero-engine discussion
Since Kavery is flat rated, does anyone know the specifics of the flat rating e.g. x kN at y altitude or something like that??
Re: Kaveri & aero-engine discussion
the flat rating in my understanding is to do with combustor ignition at high alt and stability.. like thrust drop at high ambience compensated by higher TET. so, the wet and dry kNs are maintained.
Re: Kaveri & aero-engine discussion
^^ Flat rating can be achieved in many ways. But I wanted to know what's the specification for Kaveri thrust. As an example a flat rated engine could be specified as "30kN thrust till 30000 ft" which means it will have 30kN thrust from SL to 30000ft. Whats that spec for Kaveri?? I don't remember seeing such number for Kavri in past.
Re: Kaveri & aero-engine discussion
Something very exotic has come up. TBRL has floated a tender for Liquid fuel-air mass flow rate measurement set up for pulse detonation engine.
It will be a 2.5 kN engine
. The set up specifies a 20 litre fuel tank. If the same tank is retained in the flying article, then this engine is going to power the flight for a few minutes. Therefore, if it materializes, it will be part of a weapon, not a drone!
It will be a 2.5 kN engine

Re: Kaveri & aero-engine discussion
Probably an add on booster kit for a 450/900kg bomb/PGM to extend its range.
Re: Kaveri & aero-engine discussion
Unlikely.
Re: Kaveri & aero-engine discussion
Our own Buzz bombs... 

Re: Kaveri & aero-engine discussion
The tender is for TBRL Ramgarh, which has a Rail Track Rocket Sled. Methinks the pulse detonation engines will replace the rockets, perhaps for the ability to control thrust.indranilroy wrote:Something very exotic has come up. TBRL has floated a tender for Liquid fuel-air mass flow rate measurement set up for pulse detonation engine.
It will be a 2.5 kN engine. The set up specifies a 20 litre fuel tank. If the same tank is retained in the flying article, then this engine is going to power the flight for a few minutes. Therefore, if it materializes, it will be part of a weapon, not a drone!
Re: Kaveri & aero-engine discussion
That makes a lot of sense! You may be onto something here. The fuel storage vessel and air feed vessel are to be housed on a 1M (H) X 1.5M X 1.5M movable platforms.
On the other hand, this might be a test of the engine in motion, simulated on the test track. I think the engine has been developed. Because they know the exact pressures for the air and the fuel feed mechanism.
On the other hand, this might be a test of the engine in motion, simulated on the test track. I think the engine has been developed. Because they know the exact pressures for the air and the fuel feed mechanism.
-
- BRFite -Trainee
- Posts: 31
- Joined: 11 Aug 2016 06:14
Re: Kaveri & aero-engine discussion
NRao, seems there are lot of projects DRDO is pursuing with academia, couldn't find if those projects can be tracked though.
http://www.drdo.gov.in/drdo/boards/ardb ... ojects.htm
http://www.drdo.gov.in/drdo/boards/ardb ... ojects.htm