Kaveri & Aero-Engine: News & Discussion
Re: Kaveri & Aero-Engine: News & Discussion
HAL gets new design & test facility for HTFE-25, HTSE-1200 & IMRH engine
HAL's new center is AERDC (aero engine R&D center).
Indian Defense Analysis
HAL's new center is AERDC (aero engine R&D center).
Indian Defense Analysis
Re: Kaveri & Aero-Engine: News & Discussion
Su-30 MKI as Kaveri Engine Test Bed - an idea from Air Cmde. Tapas Sen
Shared by Shiv sir, I always thought of replacing one of engine of twin-engine aircraft to test the new engine but this is ingenious of using podded Kaveri engine at one of the hard points of fighter jet like Su-30.
Looks viable and IAF/GTRE should consider it.
Shared by Shiv sir, I always thought of replacing one of engine of twin-engine aircraft to test the new engine but this is ingenious of using podded Kaveri engine at one of the hard points of fighter jet like Su-30.
Looks viable and IAF/GTRE should consider it.
Re: Kaveri & Aero-Engine: News & Discussion
So 30 is too small a platform for it to be used as a test vehicle as described in the video link above.
There is a reason why most of the engine test beds are large 4 engine platforms. With test articles mounted close to the fuselage.
Smaller 2 engine jets are also used, but as test beds for smaller engines.
https://aerospace.honeywell.com/us/en/a ... den-engine
The linked page has a picture of a 757 as an engine test bed.
The article from simple flying details what we need to know about such platforms.
https://simpleflying.com/flying-engine-testbeds/
Published on 1st Nov 2023.
There is a reason why most of the engine test beds are large 4 engine platforms. With test articles mounted close to the fuselage.
Smaller 2 engine jets are also used, but as test beds for smaller engines.
https://aerospace.honeywell.com/us/en/a ... den-engine
The linked page has a picture of a 757 as an engine test bed.
The article from simple flying details what we need to know about such platforms.
https://simpleflying.com/flying-engine-testbeds/
Published on 1st Nov 2023.
Re: Kaveri & Aero-Engine: News & Discussion
One a slightly different note, Shivji says, regarding absence of FTB for Kaveri, the following:nash wrote: ↑03 Jan 2024 11:30 Su-30 MKI as Kaveri Engine Test Bed - an idea from Air Cmde. Tapas Sen
Shared by Shiv sir, I always thought of replacing one of engine of twin-engine aircraft to test the new engine but this is ingenious of using podded Kaveri engine at one of the hard points of fighter jet like Su-30.
Looks viable and IAF/GTRE should consider it.
But IMVHO, should also have added the following, regarding absence of even basic test facilities for modern TF design and development initiatives - ref:... it remains a shameful deficit and we have to send the engine to Russia for high altitude testing ...
For ref: The useful work extracted at Kaveri's turbines would be around 20-22MW etc ...HAL is utilizing the established but limited facilities at NAL, GTRE and other DRDO labs for testing combustor, gas generator turbine, electronic components etc. However we do not have the facilities in the country to test compressors, HP turbines, power turbines of the order of 1 MW and above with matching speeds. Flying test bed and altitude test benches are the two major facilities which have to be established on case to case basis, which demand an investment of the order of 1500+ Crores. These facilities are expected to be established under the proposed AERO ENGINE COMPLEX by MoD as National Test Facilities.
Source - Refer Pg22/23
Betw this was also acknowledged way back in 2016 itself by standing committee of defense etc:
As I've said multiple times now, over last 2+ decades, the sheer level of achievement by GTRE/DMRL/MIDHANI et all, wrt ab-initio 4-Gen TF dev initiative, is absolutely stunning ...... The existing Fan & Compressor Test Facility at Gas Turbine Research Establishment (GTRE) has inadequate capacity and has become obsolete. To carry out testing of Fan & Compressor for existing and future generation gas turbine engine programmes of GTRE, it is essential to have a dedicated Fan & Compressor test facility at GTRE ...
Ref: STANDING COMMITTEE ON DEFENCE (2016-17) - Recommendation (Para No. 26)
However, appreciating it, requires some basic level of technological understanding what TF dev entails etc, as there's no concept of shiny-brochure etc from these sarkari depts/labs/orgs.
For example, just a few posts back there's an url shared wrt M-88 etc - careful analysis and study would have revealed that MIDHANI (or was it DMRL) have already patented (jointly, with Safran), back in 2017-18, productionising of Y-TiAl based LPT blades etc.
(Pls refer to my earlier posts, if you are interested in understanding the relevance of it ...)
I'm sure all these expertise would be frittered away, without any budgetary support and any actual program to implement them (a decade was lost not even attempting to platform-fly-test and baseline the basic TF design etc).
Oh well ...

Re: Kaveri & Aero-Engine: News & Discussion
Why is the MOD and GOI extremely shortsighted when it comes to this program????!!! For fvcks sake get the necessary 4 engine flying testbed and the other facilities needed. India has a need to purchase at least 2k engines!!!! Why do these babus insist on dragging this out in piecemeal fashion for literally everything??
Last edited by Rakesh on 03 Jan 2024 22:21, edited 2 times in total.
Reason: Please watch your language
Reason: Please watch your language
Re: Kaveri & Aero-Engine: News & Discussion
The idea that either the French or the Russians will give an unbiased opinion of a product (in the case of Kaveri) is silly. They have already shown that when they expect India to fund their research, not its own. I am referring to the sale of Vikramdita and Safran's "work" on upgrading the Kaveri. If India wants to be a serious developed economy, she needs to be in control of her testing.hgupta wrote: ↑03 Jan 2024 22:04 Why is the MOD and GOI extremely shortsighted when it comes to this program????!!! Forfvckssake get the necessary 4 engine flying testbed and the other facilities needed. India has a need to purchase at least 2k engines!!!! Why do these babus insist on dragging this out in piecemeal fashion for literally everything??
This will be expensive and there will be errors, but as long as one is prepared to learn from mistakes, it is part of the learning process. There will be opposition from those who stand to lose - be it civil servants or military who lose jaunts (and possibly more) to foreign shores. Once the Election is done that is a decision that the Gov has to make.
Re: Kaveri & Aero-Engine: News & Discussion
Maitya, A few questions from.an observer.
1) What is overall compressor efficiency at sea level standard MIL Thrust?
2) Why is stage pressure ratio so low (~1.4) if low pressure compressor and fan are transonic, shouldn't those be much higher?
3) What is the shaft rpm of the compressor stage
1) What is overall compressor efficiency at sea level standard MIL Thrust?
2) Why is stage pressure ratio so low (~1.4) if low pressure compressor and fan are transonic, shouldn't those be much higher?
3) What is the shaft rpm of the compressor stage
Re: Kaveri & Aero-Engine: News & Discussion
ramanaji, I (or anybody outside GTRE etc) don't have access to Compressor Map etc of Kaveri/Kabini (and rightly so) to accurately answer these questions, however from whatever has been revealed publicly (in various seminars and papers etc) over last 2+ decades, the following is what we know:ramana wrote: ↑04 Jan 2024 09:24 Maitya, A few questions from.an observer.
1) What is overall compressor efficiency at sea level standard MIL Thrust?
2) Why is stage pressure ratio so low (~1.4) if low pressure compressor and fan are transonic, shouldn't those be much higher?
3) What is the shaft rpm of the compressor stage
1) What is overall compressor efficiency at sea level standard MIL Thrust?
I think the HPC efficiency is
Fan/LPC - 3 stages, 3.40 pressure ratio, Surge margin>20.
HPC - 6 stages, 6.42 pressure ratio, Surge margin>21.6 (Corr tip speed - 370m/s)
Combustor - efficiency >99% - pattern factor of 0.35 and 0.14
2) Why is stage pressure ratio so low (~1.4) if low pressure compressor and fan are transonic, shouldn't those be much higher?
Yep, agree the SPR of 1.4 (think the avg is ~1.5 actually) is slightly lower than what we'd expect from a transonic blading design (in contrast, F404 has 4.1 Fan/LPC PR, so avg SPR of ~1.6) but I guess it's more of a design choice, especially wrt the flat-rating requirement etc.
More on this in the later part of the post ...
3) What is the shaft rpm of the compressor stage?
This is not directly published in open source, anywhere that I've noticed so far, but I've seen some very old references (and I don't have links etc of them), so pls take it FWIW - Kaveri LPC 10312rpm (13200rpm for F404 Fan/LPC).
But, but, it'd be nice if this "observer" of yours, if he graces this forum again, and participates actively - it was always, and will remain, a pleasure and learning experience for all of us here - after all, he must have got bored enough with Yak herding by now.

Least he can do is critique this 5 part series, from a few pages back:
Part -1
Part -2
Part -3
Part -4
Part -5
Anyway, coming back to the above question (No 2) wrt Kaveri's lower Fan SPR, whilst it being a transonic one, pls note:
As we all know, the Fan/LPC PR is tightly coupled with the mass-flow rate that the designed core can handle - so, if the core design needs a certain mass-flow volume to allow for a flat-rating, and if the inlet geometry would allow a certain mass-flow only, then the Fan/LPC PR (and the BPR) would have to be adjusted accordingly. IOW if the core mass-flow have to be kept unaltered, then increasing the Fan SPRs will require redesigning the inlet geometry and allow for higher BPR.
This since, increasing the mass-flow thru core, without increasing the TeT levels, will result in actually lower thrust extraction etc (pls refer to the gyan thread and various graphs that I'd posted almost decade plus back) - which is basically a whole new design.
I mean, Fan/LPC/HPC SPR is a function of majorly two factors:
1) RPM
2) Blade design
(there are multiple other factors like blade surface roughness, flow leakage, incidence angle, inlet pressure distortion levels, flow distn across blade etc etc etc, but let's not go there. Betw flow leakage can be controlled by sophisticated methods like wall bleeding, tip injection methods etc - not in scope for a forum discussion like this).
Now, if we assume the blade design to be contemporary, which I think it is, designing for a higher Fan stage SPRs (and thus Fan PR) via increased RPM route, would thus require tinkering with the LPT. One of the option is to make the LPT lighter, either via usage of different materials (like CMC or γ-TiAl (as in M88) - refer to my prev posts), or via diff manufacturing tech like Blings (or atleast Blisks) or both. Also need to keep in mind the Fan/LPC surge margin levels, as it will be hit if the RPM etc are willy-nilly increased (and chocking the Compressor) etc.
So summary is, and sorry for going of an tangent, given the flat-rating rating requirement and the material (and manufacturing) constraints of the HPT (and to a lesser extent the HPCs as well), the Fan/LPC SPR and PR levels were chosen/frozen at the design itself.
But that doesn't mean, it can't be improved (it should be) but that would need extensive changes to all downstream systems/components. In fact, read somewhere (can't remember where, it has been a while now), in the K10 series GTRE were contemplating 4.1 PR levels for the Fan/LPC. But a decade went by without flight-testing and baselining the K9, any talk of K10 etc is simple utopia.
Last edited by maitya on 05 Jan 2024 18:16, edited 1 time in total.
Re: Kaveri & Aero-Engine: News & Discussion
Thanks for the detailed answers.
Observer remains incognito. It's not N^3.
Observer remains incognito. It's not N^3.
Re: Kaveri & Aero-Engine: News & Discussion
Next set of questions:
Why is the compressor efficiency so low? LPC, 85%, HPC 85% cited by GTRE. Those imply a polytropic efficiency under 88%, whereas textbooks in the 1980s cited 92%.
What keeps our efficiency so low and have they not tried to boost that?"
Why is the compressor efficiency so low? LPC, 85%, HPC 85% cited by GTRE. Those imply a polytropic efficiency under 88%, whereas textbooks in the 1980s cited 92%.
What keeps our efficiency so low and have they not tried to boost that?"
Re: Kaveri & Aero-Engine: News & Discussion
Dhanyawaad Maitya ji for sharing what you know
Re: Kaveri & Aero-Engine: News & Discussion
So SCB is a red herring, the root issue is elsewhere.chetak wrote: ↑15 Jun 2023 12:10a few organizations in India are already doing thissanman wrote:
The Hot part of the engine, and the single-crystal turbine blades are the most crucial, and most difficult to master.
We won't be getting that tech transfer as part of this deal.
but one would hesitate to say if the technology has been mastered in a general way and therefore, is capable of being adapted to various engines under development or they are doing it from ready made kits which have all the materials required and is being used merely as a technology demonstrator to develop the skill sets required.
Some speculate it's hot section, but good engineer can with public available daya peer through the GTRE kimono. Could be area other than hot section !

I lost my confidence in GTRE in 2006 after many royal screw-up on commitments.
Still remember the GTX engine cutout in Aero India ~2005 just opposite the Bharat- Rakshak stall.
Re: Kaveri & Aero-Engine: News & Discussion
Folks let's keep it technical.
A good to and fro is going on.
A good to and fro is going on.
Re: Kaveri & Aero-Engine: News & Discussion
Ramanaji, here's a small comparo of various perf parameters of the other contemporary 4th Gen military TFs wrt Kaveri:

For such a small BPR design, juxtaposed with such high mass-flow-rate (which essentially means a much larger vol of mass-flow thru core), I would say achieving such compressor efficiency figures is actually top-notch achievement. As, higher mass-flow thru core results is higher Secondary losses (higher aerodynamic losses due to flow instabilities via boundary layer separation etc), reducing overall efficiency.
Textbooks normally would site whatever is theoretically possible/available, but in real life these perf parameters are heavily dependent on the various design constraints that are forced upon by (many a times even competing) requirements.
I don't want to belabour the Flat rating requirement etc, but if your design-allowance is for higher vol of mass-flow air thru core, then HPC efficiency would have to take a hit (by design), I'm afraid.
Also, HPC efficiency of 85% (and 87% for Fan/LPC) is nothing to scoff about betw - when the super-duper M88-2 figures (published!!) stands at - Compressor efficiency (ne): 0.89 - Fan efficiency (nf): 0.91.
Plus, for a military turbofan, the HPC (and Fan/LPC) efficiency parameters, though quite important, but not as much as the dry thrust (and weight and transient response*) requirements.
(*e.g. transient engine responses to rapid changes in thrust and torque commands at constant fan speed)
SFC is also a very important requirement, mind you, and it is this parameter that is directly/majorly impacted by these turbine efficiency figures.
But if you compare the dry SFC values above, you'd know, Kaveri compressor efficiencies (both Fan/LPC and HPC) are more than adequate (actually is an over-achievement) towards achieving dry thrust, SFC etc.
(transient response parameters are classified, so wouldn't know)
Either way, summary is, Kaveri does a more-than-decent job wrt these turbine efficiency figures when compared to other contemporary 4th Gen military TFs.
But but, that doesn't mean I'm saying, that these .85 (and .87) compressor efficiencies shouldn't be worked upon or improved - they certainly should be. IMVHO, 2-3% point improvement is well within GTRE etc reach, but without any funding not sure how much focus is there of such aspects.
For example, there are very well known aspects that influences these efficiencies:
Blade Surface smoothness, Groove Casing Technique, Tip Injection etc are well known/established factors that one should be looking into.
Compressor fouling caused by surface roughness is a prominent loss in transonic axial flow compressors, which directly impacts the compression ratio - and it's a published fact that compressor efficiency increases from 89% to as much as astronomical 94% etc, when the blade surface roughness decreases from 0.5 μm to 0.2 μm.
This is because, the roughness of the blade surface creates a distortion effect on the flow path, which increases the shock wall at the leading edge and tip vortices at the trailing edge.
Question is, do we have these technologies (for example laser shock peening) to bring-in such improvements - earlier may not be, but now most probably it has been developed inhouse.
(not sure if they are matured to scale-manufacturing levels etc, though)
Similarly, Groove casing techniques are heavily influenced by the Tip Clearance values (as a % of rotor tip Chord values), but implementing in a mass-manufacture mode will be a steep challenge.
I think I should stop here, but before I do that, I'd urge you to go thru these slides from Webinar on Aero Gas Turbine Engine Development in India - 2022, posted by Rakeshji a few pages back.
Re: Kaveri & Aero-Engine: News & Discussion
https://idrw.org/taking-flight-together ... e_vignette
Published on 30th December.
We seem to have missed this news.
With Godrej being selected for the fabrication of dry Kaveri for the UCAV program. I think that this tie-up will bear great results.
Published on 30th December.
We seem to have missed this news.
With Godrej being selected for the fabrication of dry Kaveri for the UCAV program. I think that this tie-up will bear great results.
Re: Kaveri & Aero-Engine: News & Discussion
Maitya, Thanks for the detailed reply.
So low bypass ratio and increased mass flow rate are causing low TeT. Yet dry thrust is comparable in that class.
Low BPR is for flat rating and am sure the other super duper engines become asthmatic in different airfields. So don't change it.
What is the way to improve TeT for that holds the key?
Ceramic blades?
My gut feel is the fan and compressor hold the key.
How to get 100 deg C boost to TeT?
Keeping same BPR.
Need to improve Fan/LPC pressure ratio from 3.4 to higher.
So low bypass ratio and increased mass flow rate are causing low TeT. Yet dry thrust is comparable in that class.
Low BPR is for flat rating and am sure the other super duper engines become asthmatic in different airfields. So don't change it.
What is the way to improve TeT for that holds the key?
Ceramic blades?
My gut feel is the fan and compressor hold the key.
How to get 100 deg C boost to TeT?
Keeping same BPR.
Need to improve Fan/LPC pressure ratio from 3.4 to higher.
Re: Kaveri & Aero-Engine: News & Discussion
Fighter jet engine deal with India to start this year: GE Aerospace's Amy Gowder
https://economictimes.indiatimes.com/ne ... 676912.cms
10 Jan 2024
https://economictimes.indiatimes.com/ne ... 676912.cms
10 Jan 2024
Re: Kaveri & Aero-Engine: News & Discussion
Ramanaji, I'll respond to you in a while ... however this is quite big:
Reg: SCB for Kaveri Dry Engine
However the SCB used in HAL helicopter HPT blades are solid (similar to those used in AL-31FP etc), so no great shakes ... but let's see!!
Reg: SCB for Kaveri Dry Engine
However the SCB used in HAL helicopter HPT blades are solid (similar to those used in AL-31FP etc), so no great shakes ... but let's see!!
Re: Kaveri & Aero-Engine: News & Discussion
Maityaji, noob pooch - How are SCB microdrills/microvents made? Is it still single crystal? (are SCB blades truly just one crystal?) If there are any links where i can read up on this, that should be plenty.maitya wrote: ↑12 Jan 2024 20:47 Ramanaji, I'll respond to you in a while ... however this is quite big:
Reg: SCB for Kaveri Dry Engine
However the SCB used in HAL helicopter HPT blades are solid (similar to those used in AL-31FP etc), so no great shakes ... but let's see!!
Dhanyawad
-
- BRF Oldie
- Posts: 4104
- Joined: 30 Jul 2004 15:05
- Location: Spectator in the dossier diplomacy tennis match
Re: Kaveri & Aero-Engine: News & Discussion
https://www.youtube.com/watch?v=1tM96B77n0Uernest wrote: ↑13 Jan 2024 03:49Maityaji, noob pooch - How are SCB microdrills/microvents made? Is it still single crystal? (are SCB blades truly just one crystal?) If there are any links where i can read up on this, that should be plenty.maitya wrote: ↑12 Jan 2024 20:47 Ramanaji, I'll respond to you in a while ... however this is quite big:
Reg: SCB for Kaveri Dry Engine
However the SCB used in HAL helicopter HPT blades are solid (similar to those used in AL-31FP etc), so no great shakes ... but let's see!!
Dhanyawad
Re: Kaveri & Aero-Engine: News & Discussion
https://idrw.org/indias-kaveri-engine-e ... k1a-fleet/
Talks of a new after burner that'll take "kaveri 2.0" to get to a wet thrust of 83-85kn
Talks of a new after burner that'll take "kaveri 2.0" to get to a wet thrust of 83-85kn
Re: Kaveri & Aero-Engine: News & Discussion
As per the earlier reports, the present version itself has greater thrust than anticipated/calculated. We can be sure this 8.5-ton thing maybe even better than that target thrust. But testing in Russia may be a big issue. Do we have any alternatives?
Re: Kaveri & Aero-Engine: News & Discussion
Why can't India build its own testing facilities???
Re: Kaveri & Aero-Engine: News & Discussion
The technique shown in the video is called super drilling and is more of an Electrical Discharge Machining that it is drilling. This is a fairly straight fwd process and is fairly common and the hardness of the target material does not matter.
The uber advanced part is to get shaped cooling holes in the turbine blades. A GE engineering was mentioning that GE India is not allowed to design or discuss the details of the shaped cooling holes of a turbine blade as it is still export controlled tech in the US.
Re: Kaveri & Aero-Engine: News & Discussion
Kailash wrote: ↑13 Jan 2024 15:58 https://idrw.org/indias-kaveri-engine-e ... k1a-fleet/
Talks of a new after burner that'll take "kaveri 2.0" to get to a wet thrust of 83-85kn
Our lurker is now looking at the after burner.
Long ago in Aero Expo thread a cutaway diagram of Kaveri was posted.
What is needed is the length the After burner section?
So far the fan and compressor are not giving the required TeT and could improve smoothness and reduce 3-D shocks.
Let's see.
Re: Kaveri & Aero-Engine: News & Discussion
Why learnings from the Kaveri can't be used as a base for the future in country turbofan effort for the AMCA and beyond?
More importantly, what will it take to translate the learnings into the next generation engine development effort.
More importantly, what will it take to translate the learnings into the next generation engine development effort.
Re: Kaveri & Aero-Engine: News & Discussion
Like he is working on the after burner or just calculating math for it for BR consumption?ramana wrote: ↑16 Jan 2024 00:14Kailash wrote: ↑13 Jan 2024 15:58 https://idrw.org/indias-kaveri-engine-e ... k1a-fleet/
Talks of a new after burner that'll take "kaveri 2.0" to get to a wet thrust of 83-85kn
Our lurker is now looking at the after burner.
So far the fan and compressor are not giving the required TeT and could improve smoothness and reduce 3-D shocks.
Let's see.
Re: Kaveri & Aero-Engine: News & Discussion
Looks like Kaveri is near its goal. No wonder unkil wants to set up its engine before kaveri is proven and put a stop to it.
Similar Stryker is on offer when WhAP is getting ready.
Similar Stryker is on offer when WhAP is getting ready.
Re: Kaveri & Aero-Engine: News & Discussion
Ramanaji, Fan and Compressor has nothing to do with TeT increment - if HPT TeT have to be improved, it can be done by working/changing the HPT blades (and maybe the disc as well).ramana wrote: ↑16 Jan 2024 00:14Kailash wrote: ↑13 Jan 2024 15:58 https://idrw.org/indias-kaveri-engine-e ... k1a-fleet/
Talks of a new after burner that'll take "kaveri 2.0" to get to a wet thrust of 83-85kn
Our lurker is now looking at the after burner.
Long ago in Aero Expo thread a cutaway diagram of Kaveri was posted.
What is needed is the length the After burner section?
So far the fan and compressor are not giving the required TeT and could improve smoothness and reduce 3-D shocks.
Let's see.
( actually it is, but it's quite nuanced, and I'll touch upon it towards the end of the post)
Just as an example, using suddha-desi DMS4 Ni-Superalloy based 4th Gen HPT blades should be able to give 1500+ deg C TeT levels - provided, the cooling architecture of the blades are improved upon. Just changing the HPT blade metallurgy, without corresponding change in the blade cooling technology, will not be much of an help, and the full advantage of such a change wouldn't accrue.
(there are aspects like thin-wall properties of SC casting etc, which is where the real advantages accrue, not merely on the bare metal temp handling capability - again something that I've posted multiple times earlier)
A 4th Gen SC Ni-Superalloy, eg DMS4, provides about 60-70deg C advantage (wrt the raw-metal temp capability), over a 4th Gen DS Ni-Superalloy (e.g. again suddha-desi DMD4).
So what it means is, Kaveri's DS Ni Superalloy already provides 1020-1050deg C raw-metal temp capability - graduating to a 4th Gen SC Ni-Superalloy, will take it to 1100-1110deg C capability.
Between, that's absolutely cutting-edge tech as it gets, and is world-beater capability.
It needs to be noted here-in as well, that just by increasing the raw metal temp capability, beyond a point, will mean lesser and lesser advantage-accruement from the 7-8Ysz based TBC coating etc.
As, under CMAS attack these 7-8YSZ based top-coat TBC applications allows for a maximum surface temperature capability of about 1200-1250deg C. Pls refer to my earlier posts here, for details.
But I've still not understood the need of increasing HPT TeT levels etc - current K9 Gas Generator works perfectly fine for the intended application, so why change it? The issue is with the AB, so a new design is required there - not so in the Gas generator.
(there can be some issue wrt the PR of the LPT, which may impact the AB design, but will delve into it on some other day).
Anyway, increasing TeT levels of a TF, has more to do with NGV casting technological capability etc, and less to do with HPT blades .
After all, the advertised TeT levels are actually experienced by the NGVs (and not the HPT blades) first hand - by the time, the hot gas from the combustor exit reaches the HPT blades, after passing thru the NGV blades, already quite a bit of temp drop has accrued. Typically, the Turbine Rotor Inlet temp, that is relevant to HPT blades, is 80-100deg C lower than TeT.
So just as an example, and without naming names, say a 4th Gen TF "advertises" TeT level of 1542deg C - that means it's NGV blades needs to be capable of withstanding 1540-1550deg C operating temp levels, while the HPT blades would quite well at 1440-1450deg C levels (also called Turbine Rotor Inlet temp capability).
Thus, handling higher TeT levels are more of function of the NGV blade casting/metallurgy capabilities - and less of HPT blades. I mean, if willy-nilly the HPT blades are changed and be made capable of higher TeT levels, it will not be of too much of an help, if NGV blades are not proportionately improved.
However, NGV blades have an advantage - the are static (unlike HPT), so the centrifugal forces (~150-200MPa levels experienced by the HPT blades) issue is not there. So it’s primary focus is towards handling of thermal shock (aka thermal fatigue performance) and ofcourse oxidation and environmental corrosions issues. It also needs to account for high thermal stresses resulting out of anisotropic (different level of expansion in different directions) thermal expansion of the larger (relatively) vane blade structures.
IOW, quite a different set of technological challenges.
Otherwise, all its internal and external cooling requirements are much higher than the HPT blades - there was a time when Cobalt based superalloys were used (experimented with, worldwide) for NGV, due to their intrinsic higher thermal resistance capability (but much lower thermo-mechanical capability). e.g FSX-414 in GE F414.
But they are quietly abandoned and moved onto first DS and then to SC ones - so for example, for F414, GE chose: FSX-414 -> DS GTD-111 (and later DS GTD-222) -> to now maybe to SX Rene N6 (not published publicly).
(Do note GE still uses FSX-414 for its electric turbine applications)
Anyway, hi-fi 4th Gen TFs like M88-2, EJ200, F414 all uses the same SC Ni-Superalloy (casted) for NGV blades, as that of their HPT Blades - Kaveri uses DS NGV blades.
And there-in lies the issue - note NGV blades are an order of magnitude larger than HPT blades. And larger SC casting is notoriously difficult to cast.
(LAB effect etc, refer to my previous posts on this a few pages back - DS casting of larger blades is not that difficult betw).
So, I seriously doubt we have developed indigenous capability to mass-manufacture this level of 4th Gen SC HPT, and the larger NGV, blades ... I've written extensively on this, for many years now, so will not belabour it anymore.
(Hint of course is, decade plus struggle of DMRL/GTRE/MIDHANI et all wrt the Ceramic Core fabrication for the Kaveri core manufacturing. Earliest Kaveri cores had Ceramic cores imported from SNECMA et all) - it has been claimed, by prasadji et all, that this aspect has now got resolved almost decade back)
Last but not the least, pls pls refer to this diagram (posted approx 1.5 decade back).
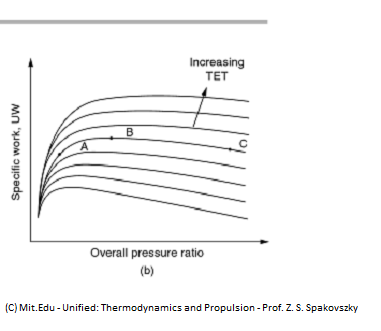
So, willy-nilly increasing the HPT TeT may become counter-productive (aka Work extraction at HPT stage can actually reduce) if OPR is not proportionately enhanced. And for a low BPR TF like Kaveri, this essentially means improvement to HPC efficiency levels.
Which is where things become really difficult wrt HPC blade design improvement, reducing secondary losses, casing treatment, blisks (atleast for the larger first 3 stages of the HPC - maybe even blings), usage of Y-TiAl for the last HPC stage, bilayer TBCs etc etc etc etc.
All pure 5th Gen TF technological stuff ... not sure if we are technologically there or not.
Already a long post, so I'll stop here ...
Re: Kaveri & Aero-Engine: News & Discussion
Since Kaveri almost achieved the required dry thrust and failed the wet thrust requirements, could the A/B issue be due to the low bypass ratio ? ie, could it be because not enough bypass cold air is going into the A/B section ?
Re: Kaveri & Aero-Engine: News & Discussion
srin-ji, you know, I feel everything about Kaveri specifications were, for some reason, all trying to achieve world-beater specs.
I mean pls refer (in the table that I'd posted a few posts above) to the other hi-fi super-successful 4th Gen TFs i.e. M88-2 and EJ200s. You'll notice both are trying to achieve, as a part of their wet thrust requirements, a modest 50% thrust growth over dry-thrust requirements.
Going by the same logic, Kaveri's wet thrust rating should have been 75KN levels (dry being 51KN), which it actually achieved, isn't it ... but no, the requirement has to be 81KN, a 60% + thrust increment requirement. Maybe, since it's copy-paste of F404 requirement, that's why.
Now, it's not as simple as dumping more fuel to the LPT exhaust and increment the thrust levels etc - there's some level of efficiency required from the combustion there, which in turn requires adequate amount of stagnation pressure from the LPT exit.
Now that tells me the LPT efficiency (so in a way, it needs to extract more work) needs to go up, so that exhaust velocity of the mass-flow, post LPT, reduces (thus increasing the Stagnation Pressure).
But that's an holy grail again - as that would mean making the LPT blades lighter, and we enter the never-ending spiral of CMC (or atleast Y-TiAl ones like in M88-2) blades, like in latest versions of F414 etc (5th Gen TF stuff).
I'll stop here, but will revisit this in a while ...
Re: Kaveri & Aero-Engine: News & Discussion
When the program was de-linked from the Tejas, their was a curious statement that Kaveri can never power a combat LCA. Makes me wonder if the thrust requirement for Tejas changed after the engine was designed.maitya wrote: ↑17 Jan 2024 00:14 Going by the same logic, Kaveri's wet thrust rating should have been 75KN levels (dry being 51KN), which it actually achieved, isn't it ... but no, the requirement has to be 81KN, a 60% + thrust increment requirement. Maybe, since it's copy-paste of F404 requirement, that's why.
Re: Kaveri & Aero-Engine: News & Discussion
Use the 75kN Kaveri for LCA SPORT variant. LIFT role won’t require the full 81+kN for Mk1/A combat.
Re: Kaveri & Aero-Engine: News & Discussion
I missed responding to the highlighted part, in my previous post ... where-in I've dealt wrt increasing TeT of the HPT etc.ramana wrote: ↑11 Jan 2024 07:19 ...
So low bypass ratio and increased mass flow rate are causing low TeT. Yet dry thrust is comparable in that class.
Low BPR is for flat rating and am sure the other super duper engines become asthmatic in different airfields. So don't change it.
What is the way to improve TeT for that holds the key?
Ceramic blades?
My gut feel is the fan and compressor hold the key.
How to get 100 deg C boost to TeT?
Keeping same BPR.
Need to improve Fan/LPC pressure ratio from 3.4 to higher.
(as noted in that post, 100deg C TeT increment maybe difficult, but 50-60deg C is doable, given the SC Casting options available indigenously).
But Ceramic blades will not help much wrt HPT blades/vanes ... as technologically, there are significant challenges still needs to be overcome wrt durability of the CMC components beyond operating temperatures of ~1300deg C.
(Current Kaveri HP NGV operates at around 1455deg C etc).
However, with EBC coatings on CMC components the temp regime will be higher - for example, almost a decade back, there were active research going on in NASA wrt EBC coatings for SiC/SiC CMC Combustor liners (thick coatings, for surface temp levels of 1650deg C) and HPT Vanes (thin coatings, 250micro m, for surface temp levels of 1350deg C). Not sure how much of these have propagated to actual mass-production levels etc.
Various advanced fibre tech (example dense Si-free matrix) was also in active R&D mode.
But wrt moderate temp regimes (around ~900-1000deg C etc) of say LPT blades/vanes (also in shrouds etc), that's certainly an option. As mentioned before GE have already demoed (and be using them as well) in the LPT of its various products (say F414-EPE).
CMCs with almost 1/4th density of Ni-Superalloys does provide substantial weight (and other perf) improvements.
However IMVHO, I have a doubt (need to put into my TF-estimator excel tool etc to verify), that given the low bypass massflow of Kaveri (due to low BPR) this would accrue any significant benefits in terms of dry thrust increment levels.
Yes, with a lighter LPT complex, the Fan/LPC PR would go up (may even reach 4:1 levels), as it's rpm would go up - which in turn would increase the bypass gas exhaust velocity, increasing dry thrust levels etc - which indeed is the preferred route for most of global TF thrust growth programs.
(e.g M88-3 program, now cancelled - pls refer to my earlier post wrt this).
But given the anemic nature of bypass mass volume (function of low BPR) of Kaveri, I doubt this will impact the dry thrust levels any significantly.
So, majority of any dry thrust increment in Kaveri will still have to driven by the higher HPT TeT path/regime.
Another, purely hypothetical option, is to increase the BPR without impacting the core mass-flow - which means catering for additional mass-flow at the Fan face itself but that would mean inlet design/dia etc change.
Do note, in the F404 to F414 "evolution" GE did just that.
(F414 fan is 13cm larger than that of F404, increases the engine airflow by 16% etc)
Re: Kaveri & Aero-Engine: News & Discussion
Now that we are working with the designs of LCA MK2 and AMCA. Would it be a good choice to increase the fan size and hence the BPR on the Kaverimaitya wrote: ↑17 Jan 2024 12:41 Another, purely hypothetical option, is to increase the BPR without impacting the core mass-flow - which means catering for additional mass-flow at the Fan face itself but that would mean inlet design/dia etc change.
Do note, in the F404 to F414 "evolution" GE did just that.
(F414 fan is 13cm larger than that of F404, increases the engine airflow by 16% etc)
Re: Kaveri & Aero-Engine: News & Discussion
SidSomji, I think you got the nomenclature slightly wrong - an ultra low BPR TF like Kaveri is what "leaky TF" would be. Increasing BPR would propel it towards a "low BPR" TF, I guess. Anyway, these terms are just that, off-the-cuff nomenclature that has stuck.SidSom wrote: ↑17 Jan 2024 18:25Now that we are working with the designs of LCA MK2 and AMCA. Would it be a good choice to increase the fan size and hence the BPR on the Kaverimaitya wrote: ↑17 Jan 2024 12:41 Another, purely hypothetical option, is to increase the BPR without impacting the core mass-flow - which means catering for additional mass-flow at the Fan face itself but that would mean inlet design/dia etc change.
Do note, in the F404 to F414 "evolution" GE did just that.
(F414 fan is 13cm larger than that of F404, increases the engine airflow by 16% etc)to the extent where the Wet thrust can be increased to the desired levels with the same core?? i.e. with the redesign of the inlets and the provision to increase the airflow... can we convert Kaveri into a very leaky turbojet/Turbofan.?
On a serious note - food for thought:
For the F414, GE decreased the BPR to 0.25:1, from the F404 levels of 0.36:1 - why would it do so, when the overall aim was to develop a higher thrust-class TF, whilst maintaining the dimensional footprint of the F404, as much as possible.

Re: Kaveri & Aero-Engine: News & Discussion
Maybe because of higher fuel burn rate, requiring more air inside the core to maintain the fuel-air stoichiometry ratio, and also to avoid overheating of the high pressure turbine blades? This would leave less air to flow around the core.maitya wrote: ↑17 Jan 2024 19:51 On a serious note - food for thought:
For the F414, GE decreased the BPR to 0.25:1, from the F404 levels of 0.36:1 - why would it do so, when the overall aim was to develop a higher thrust-class TF, whilst maintaining the dimensional footprint of the F404, as much as possible.![]()
Re: Kaveri & Aero-Engine: News & Discussion
https://x.com/alpha_defense/status/1747 ... 97556?s=20 ---> GTRE has released an EoI (Expression of Interest) for the procurement of Ready To Fit, Equiaxed nickel alloy Low Pressure Turbine (LPT) rotor blades (450 qty) and Vane LPT sub assemblies (150 pairs) for a 80KN Engine by Indian Industries. Deliveries to start from T0 + 24 months.
Re: Kaveri & Aero-Engine: News & Discussion
There's also an video report wrt this ...Rakesh wrote: ↑19 Jan 2024 01:36 https://x.com/alpha_defense/status/1747 ... 97556?s=20 ---> GTRE has released an EoI (Expression of Interest) for the procurement of Ready To Fit, Equiaxed nickel alloy Low Pressure Turbine (LPT) rotor blades (450 qty) and Vane LPT sub assemblies (150 pairs) for a 80KN Engine by Indian Industries. Deliveries to start from T0 + 24 months.
And in that report, what is surprising is, that there are people "demanding" DS (and if possible, SC) casting tech on LPT blades and vanes. The report doesn't mention the basis of such a demand, but I suspect most of it is, to put it mildly, "buzzword"-centric.

I mean, the type of casting tech to be employed, is purely dependent of the various thermo-mechanical (TM) characteristic requirement of that engine component (in this case the LPT).
DS (or SC) casting capability comes with a price, and it may not be worthwhile to go thru all the trouble, if such TM requirements are met by equiaxed or some other mfg technology.
For example, and GTRE obviously hasn't published such detailed parameters, so we can only speculate:
For a max TeT of 1455deg C, would mean,
1) the static HPT vanes, so with no centrifugal force load, facing off such a temp profile
2) the HPT rotor blades, after some temp drop across the HPT vane stage, with be experiencing a max rotor inlet temp of say 1375-1390deg C
3) after extracting 25-26MW of work, the HPT rotor exit temp would be around 975-1000deg C
4) the static LPT vanes, again with no centrifugal force load, would continue to face-off such a temp profile
5) the LPT rotor blades, after some temp drop across the LPT vane stage, with be experiencing a max LPT rotor inlet temp of say 900-925deg C
Such operating-temp profiles (of 900-950deg C) are bang in the equiaxed Ni-Superalloy territory, but with internal blade cooling technology (another 150-200deg advantage, so asking for bare-metal capability of around 750deg C) implemented - so no great shakes.
(Just for the fun of it, you may want to google the thermo-mechanical parameters of SuperNi 115 (a MIDHANI tradename of Nimonic 115)
Anyway, for comparison sake, for F404-402, the corresponding material tech is as follows:
a) LPT blades and Vanes - Rene80, Equiaxed, Bare-metal capability of ~950deg C
b) HPT blades - Rene125, DS, Bare-metal capability of ~1010deg C
c) HPT Vanes - INCONEL MA754, it is an oxide dispersion strengthened (ODS, so produced via mechanical alloying), nickel-chromium superalloy. These possesses high yield strength at high temperature, and very good oxidation resistance, a classical requirement of HPT Vanes.
Now all these doesn't mean, DS or SC casted blades and vanes shouldn't have been used for Kaveri's LPT blades and vanes.
More so, as the Kaveri's HPT blades and vanes are DS casted only - earlier from CM247LC, now maybe from the much superior (and indigenous as well) DMD4. After all, there's not a whole world of difference between casting HPT blades (and vanes) and LPT blades (and vanes) - and in fact F414, EJ200 all uses the same route (same SC casted HPT and LPT blades (and vanes)).
(but not so with M88-2, there they chose a diff tech route of Y-TiAl for LPT applications - pls refer to my earlier post on this).
I suspect, all these dumbing-downs are for trying to match with the current Indian Industrial capabilities.
After all, there are some really difficult technological complexities that requires mastering to graduate from Equiaxed to DS (or SC) - and will list only 2 of them:
1) Casting Furnace Automation: A very high degree of automation is required for the Bridgman Casting Furnaces where-in a 4mm/hr mould withdrawal rate (resulting in a high thermal gradient of typically 4000deg K/m) is required to produce cast microstructures of dendritic form (with the primary dendrite arm spacing in the range 100–500 μm), that is essential for DS (or SC) casted structures.
Any slight deviation of these will result in various issues, one of which is misalignment of the grain boundary (wrt the blade axis).
Just as an example for a SC blade the stress rupture life (under 300MPa pressure and sustained 850deg C) is:
a) For no grain boundary mis-oreintation, so θ = 0deg : 10,000h
b) For low grain boundary mis-oreintation, so θ = 7deg : 100h
c) For high grain boundary mis-oreintation, so θ > 10deg : "few" hours, so low that not worth even reporting
2) Core Prep Technology: The technology of preparation of the cores (which implements the complex internal air-cooling passages). The material used for these cores are very dependent on the molten-metal poring temp levels (in the furnace).
So, for an equiaxed casting, just as an example, where-in the gradual solidification can be achieved by simply gradually removing the "surrounding" heat sources (which was maintaining the molten state of the superalloy), the temp can be in 1450-1500deg C levels, just above the superalloys melting point. In such cases these cores can be Silica based.
But for higher molten state applications in DS (and SC) casting scenarios, higher pouring temp is required - in the realm of 1550-1600+ deg C. At those temps, Silica based cores may not work out (high temp porosity issues) and Alumina based cores would be required.
Now, DMRL et all may have mastered such Core-prep technology, after 2+ decades of continuous failing and incremental improvements (earliest Kaveri HPT blade and vane cores were imported from SNECMA), but I doubt our domestic industrial capability would have achieved that capability.
Pls note I have had a few posts on this Core-prep technology and it's complexities, but need to search and find them to post their links again.

I'll stop here. as there are many such nuances and complexities to be considered before jumping to various casting technologies (Equi -> DS -> SC)
Anyway, the bottom line is:
A DS (or SC) casted LPT blades and vanes would have been desirable, but given the domestic industrial capabilities, an equiaxed ones would be adequate, for the time being atleast.
But but, what about using the SC casted solid-blades, for this LPT application, just like the so-called-indigenously-manufactured and oh-so-superior AL-31FP ones (of 1300+ deg C TeT fame) in Koraput. Go figure ...

Re: Kaveri & Aero-Engine: News & Discussion
https://x.com/alpha_defense/status/1746 ... 55924?s=20 ---> GTRE's 130KN TWIN ENGINE TEST BED FACILITY
The work on Civil Works and Allied Services For Engine Test Facility along with Ancillary work for GTRE at Rajankunte Bengaluru has started on 15 September 2023 meanwhile the consultacy work began in July 2023.
The deadline for the completion of all the work is October, 2025. Most of the work load has been alloted to Indian Vendors. This facility will be testing engines with Axi-symmetric nozzles and engines with Thrust Vectored Nozzles (TVN).
============================================================
Tweet below is in response to the tweet above ^^^
https://x.com/alpha_defense/status/1750 ... 31141?s=20 ---> Watch this space on 26th
The work on Civil Works and Allied Services For Engine Test Facility along with Ancillary work for GTRE at Rajankunte Bengaluru has started on 15 September 2023 meanwhile the consultacy work began in July 2023.
The deadline for the completion of all the work is October, 2025. Most of the work load has been alloted to Indian Vendors. This facility will be testing engines with Axi-symmetric nozzles and engines with Thrust Vectored Nozzles (TVN).
============================================================
Tweet below is in response to the tweet above ^^^
https://x.com/alpha_defense/status/1750 ... 31141?s=20 ---> Watch this space on 26th
